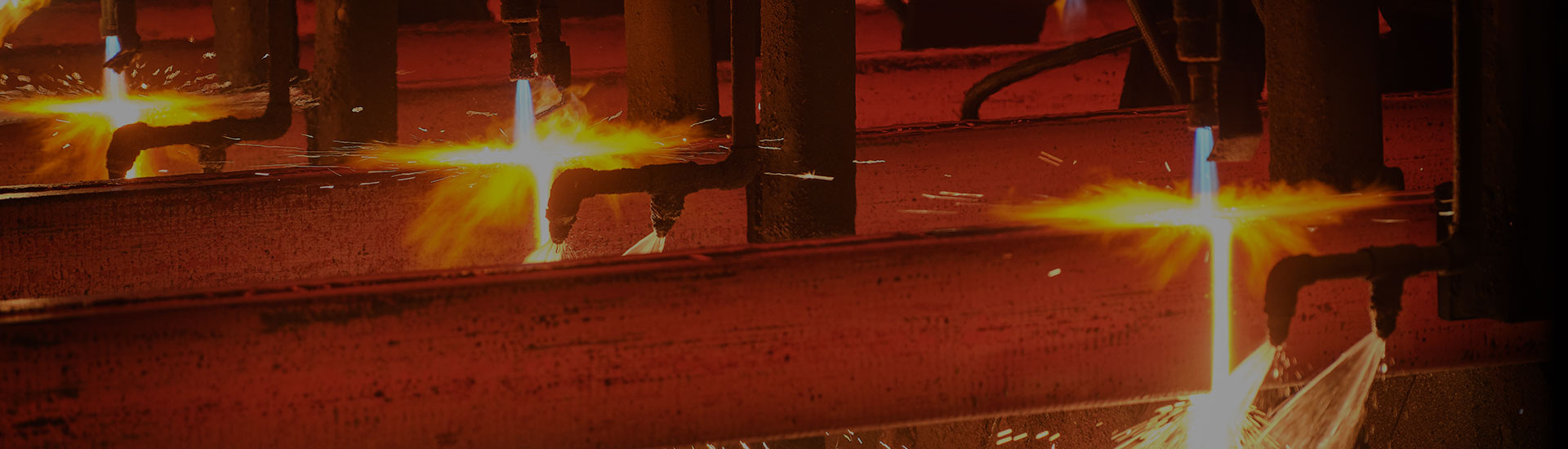
Manufacturing Process
SeAH Besteel has an efficient process layout that is optimized for high-quality product production and flexible delivery time response, from raw material management to product shipment.
Special steel (large material) production process
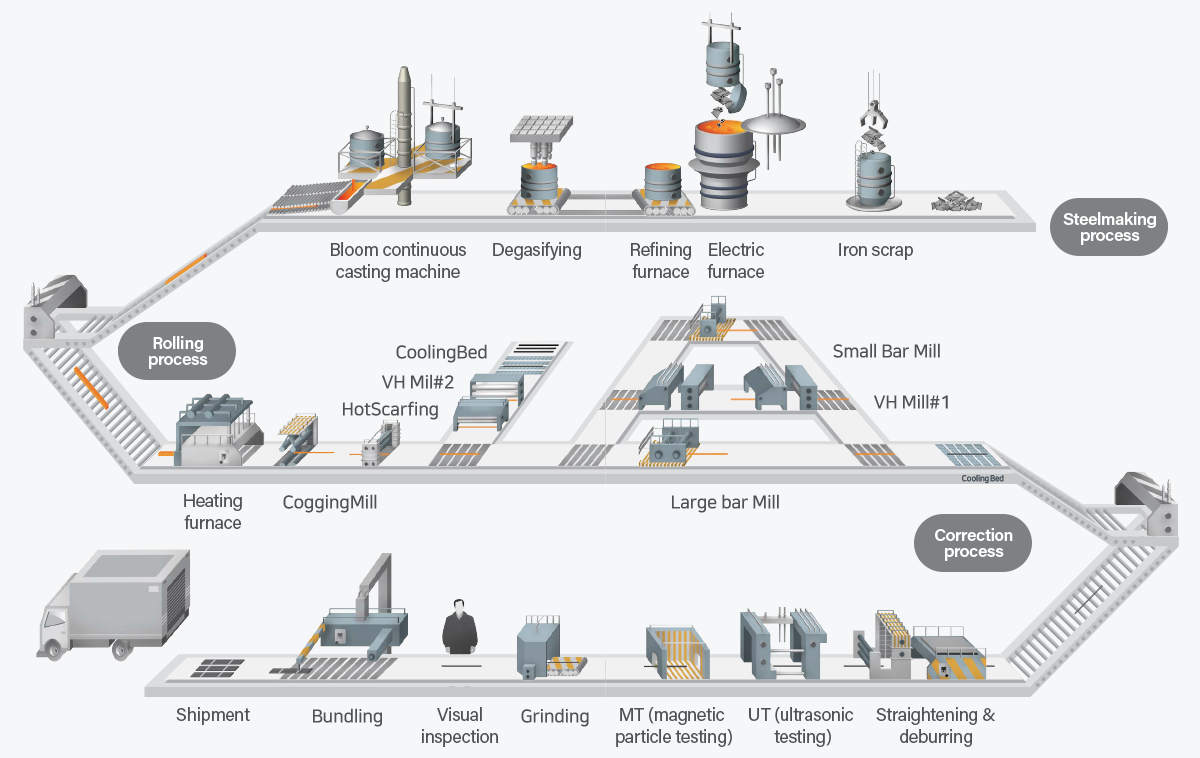
Open die forging production process
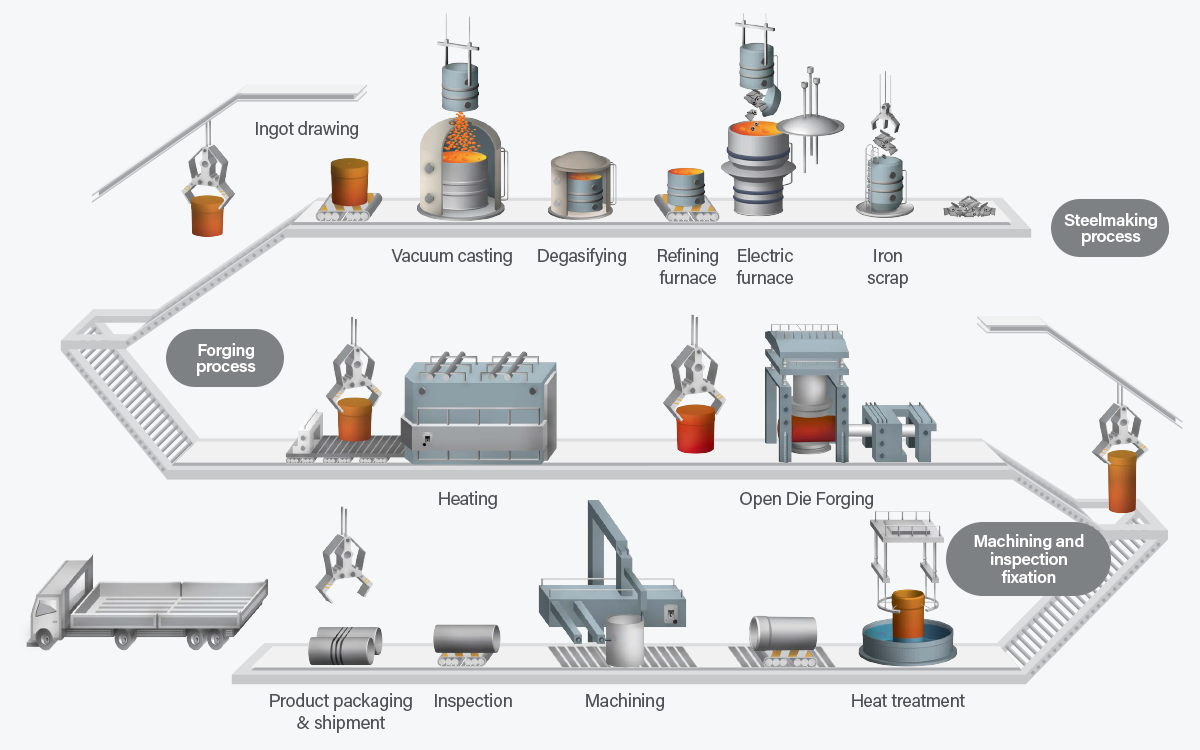
Electric Arc Fumace
Electric
furnace
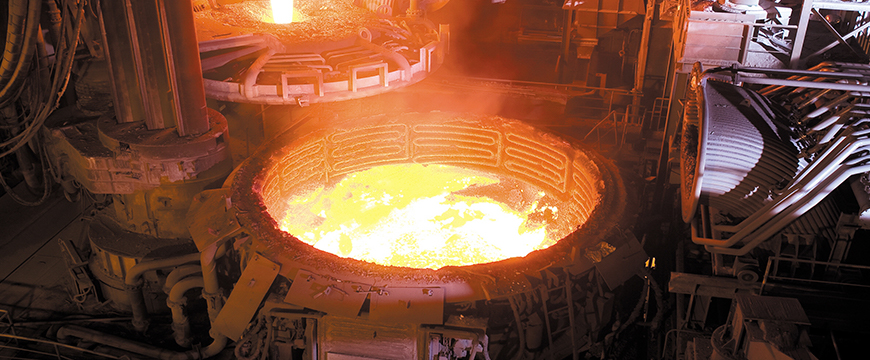
It is the first step and the core of the steelmaking process. One where iron scrap is melted by high-temperature arc heat to produce liquid molten metal. The production of stable, high-quality molten steel is an important indicator of the overall quality level of special steel products.
Rustal Heraeus · Vacuum Degassing
RH-VD
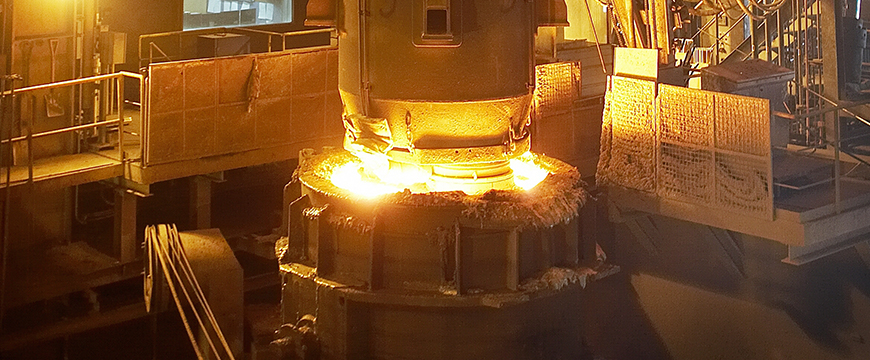
It is a facility that removes harmful gases and impurities (non-metallic inclusions) in molten steel It is an essential element for producing high-purity steel. In particular, SeAH Besteel introduced the RH facility for the first time in the domestic electric furnace industry. This improves the quality of special steel for mechanical structures This is done by removing impurities through the molten steel reflux method.
Reducing & Sizing Block
RSB
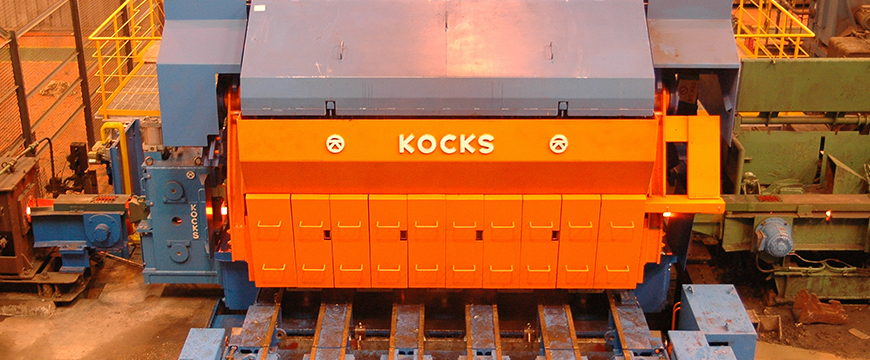
The RSB facility enables the production of products in various sizes required by customers. SeAH Besteel offers an optimal solution by combining high production efficiency and technical know-how.
Heat Treatment
Heat treatment
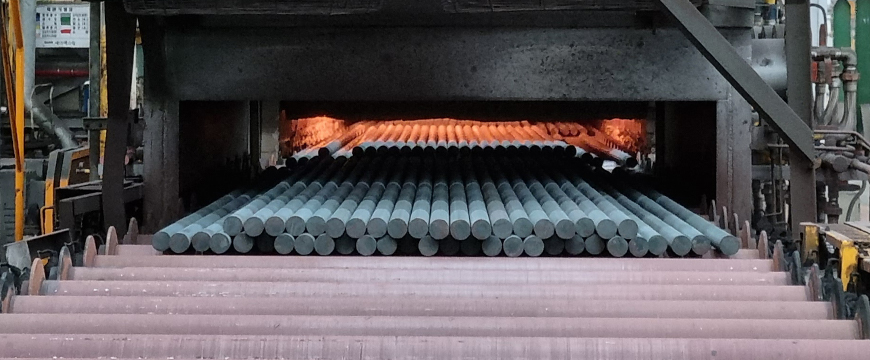
Heating and cooling processes are carried out to control the physical properties and microstructure of the rolled or forged material. SeAH Besteel's strength is its ability to design products that meet the diverse requirements of customers.
Inspection & Conditioning
Correction (inspection)
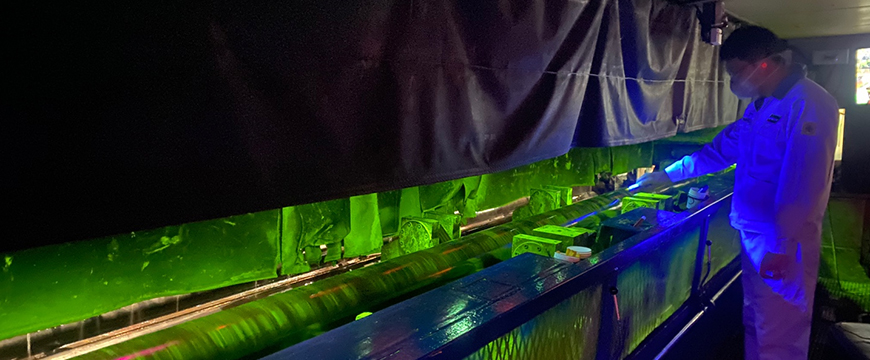
All products are fully inspected to strict standards before delivery to customers. This is done Through leakage magnetic flux inspection, magnetic particle testing, and ultrasonic testing, SeAH Besteel confirms the presence of defects inside and outside the product. It supplies products with verified quality.
Secondary Processing shop
Secondary
Machining
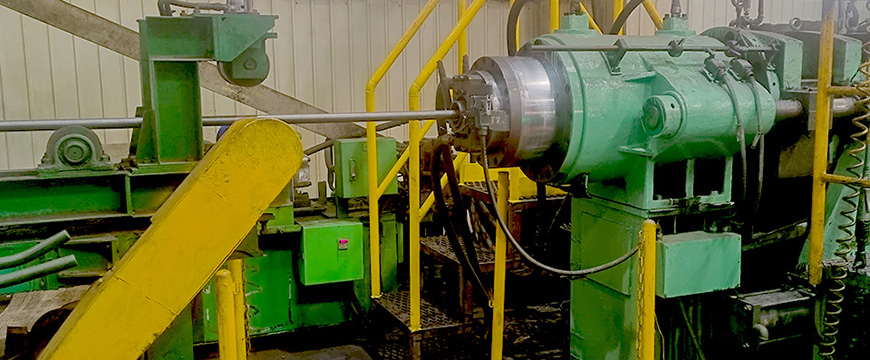
After the rolling and correction processes, the surface of the material is subjected to turning (peeling) and drawing (cold drawing) to remove surface defects. Next a process it to precise dimensions. After secondary processing, the material is used to manufacture precision machine parts.